What is wire bonding?
The conductor and wire bonding in the package is the apparatus that transfers electric current from the circuit board to the diodes. Conductors are located on the underneath or back side of the package carrier and consist of an anode and cathode division (positively and negatively charged). These pieces are manufactured from one of three different metals – Gold, Copper, silver, or even Iron. Copper Wire bonding refers to the wire bonding process that employs copper wires for interconnection, instead of the gold and aluminum wires traditionally used in semiconductor packaging.
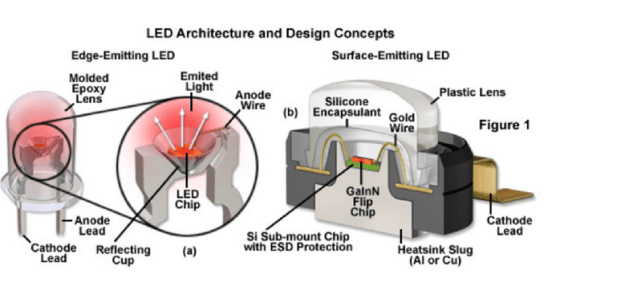
Wire bonding material
There are variances in both conductivity and environmental performance with these three metals.
Gold is the preferred metal for both situations, having both the best conductivity and being the most environmentally resistant – but as expected it is also the most expensive.
Silver/ Iron is the most susceptible to corrosion and Copper is not gold and it is unreasonable, given the different physical and chemical characteristics of each metal, to expect copper simply to bond in the same way as gold. From a performance point of view, copper can be as reliable as gold wire but copper is facing problems in more challenging stress tests such as temperature cycling, If you are in an indoor environment naturally this isn’t usually a concern with controlled, low-humidity.
For this moment, gold wire still is the more stable one for the LED display. While larger-diameter copper wire has been utilized in many applications for some considerable time, the copper bonding wire is not a ‘drop-in’ solution for gold wire and should not be seen as such in fine and ultra-fine pitch applications. Copper wire from different suppliers can differ considerably in purity and mechanical properties during the process. That is why, for small pixel pitch, normally Gold wire is adapted.
How to Choose Between Copper and Gold Wire Bonding for LED Video Displays
Copper VS Gold Copper Wire bonding refers to the wire bonding process that employs copper wires for interconnection, instead of the gold and aluminum wires traditionally used in semiconductor packaging. Copper is rapidly gaining a foothold as an interconnection material in semiconductor packaging because of its obvious advantages over gold. These advantages include:
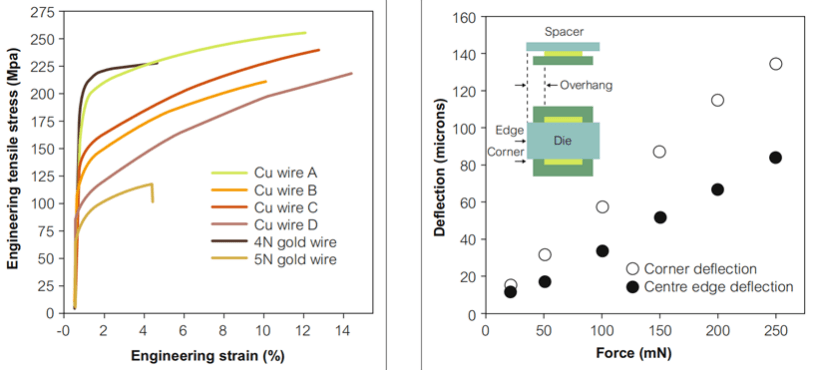
- 1) Cost reduction of up to 90%;
- 2) superior electrical and thermal conductivity;
- 3) less intermetallic growths;
- 4) Copper also has about 25% higher thermal conductivity than gold ,greater reliability of the bond at elevated temperatures;
- 5) higher mechanical stability
- The disadvantages of copper wires versus gold wires include the following:
- 1) copper tends to undergo oxidation at relatively lower temperatures;
- 2) the hardness of copper wire require bonding parameter (bond force and ultrasonic energy in particular) optimization to achieve effective bonding without causing cratering;
- 3) copper wire introduces a few failure analysis difficulties;
- 4) being relatively new, copper wire bonding technology is not yet as well-understood as gold ball bonding technology.
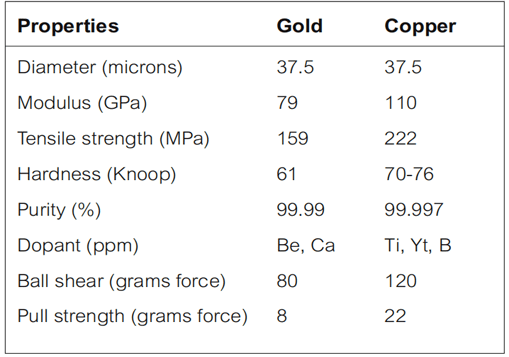
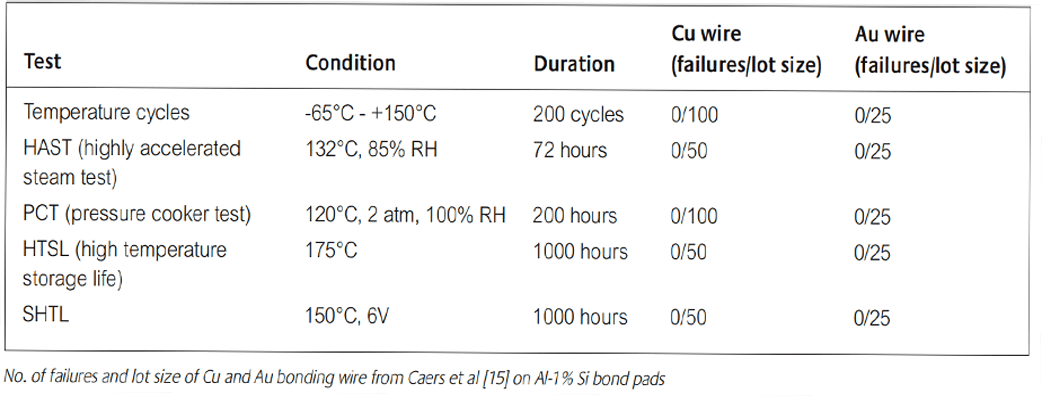
Nationstar Gold wire bonding ReeStar Series
A. ReeStar ™ (“RS”), a high-end full-color display device launched in 2013, mainly has four models, is a high-end brand of indoor foreign star high quality LED screen, more than three years warranty, excellent performance can fully realize the led high-definition display, high contrast ratio, high waterproof, high reliability, low light decay and other requirements. requirements.
B. 7 Major Performance Advantages of RS
• a). Waterproof and moisture-proof: waterproof performance reaches IPX8 level; moisture-proof performance reaches MSL 2a level.
• b). Cold and thermal shock resistance: high bonding of packaging materials, -65℃~+150℃ cold and thermal shock without dead light.
• c). Anti-back pressure: meet the high refresh frequency demand, 85 ℃, 85% RH, simulated back pressure test without failure.
• d). Salt spray resistance: the use of a wide range of simulated seaside corrosive environment without dead lights.
• e). UV resistance: UV experiments accelerated aging outdoor simulation using 3 years, light decay is less than 20%.
• f). Low light decay: high temperature and high humidity accelerated aging simulation of outdoor use for 3 years, light decay <20%.
• g). High brightness: the highest brightness level in the industry.
C. RS’s 3 Major Appearance Advantages
• a). Matte surface, high contrast.
• b). Surface luminescence technology: turn point into surface, solve the problem of led glare.
• c). Low pin technology: high cup and short foot, easy for customers to fill glue and cover mask.
D. There Are 4 Main Models
RS-1921MBAR, RS-2020MBAM, RS-2727MWAS, RS-3535MWAR
Price difference between copper wire bonding and gold wire bonding
Copper is inherently 2 to 5 times cheaper than gold, so substituting gold wires with copper wires can realize tremendous annual cost savings for a semiconductor packaging company:
let’s do simple math, you will see how much difference in price among those LED of varied bonding material: For example: P10, 10,000 Pixels/sqm with Nationstar LED 3535: Gold wire: High brightness: 20USD/K Copper Wire: Normal brightness: 10 USD/K Iron Wire: 5USD/K So Basically you can see the price difference, gold wire is about twice of copper. When it comes to indoor LED with a smaller pixel, the price can be a huge difference. if you see P2 (250,000 pixels/sqm),nationstar gold wire 1010 is roughly 8 USD/K.while copper wire is 4 USD/K. so it is about 1000 USD more. Most of the time factories /salespeople won’t tell you about the wire bonding material, unless you ask, even you ask, they can lie, because this no way you can recognize the difference by your eyes. except for chemical lab testing. Visionpi has a long term partnership with Nationstar/Kinglight, we provide verification service to our customers.
Conclusion
copper and gold wire bonding are both widely used techniques for connecting LED chips to external circuits in the LED video display industry. Copper and gold wire bonding have distinct advantages and disadvantages based on their intended use. Copper wire bonding is an economical choice that offers high thermal conductivity but has limited lifespan and low electrical conductivity. On the other hand, gold wire bonding, which is more expensive, provides thin wires and high electrical conductivity while having low thermal conductivity. Ultimately, selecting between copper and gold wire bonding should be based on the specific needs and requirements of your LED video display project.
Verification Service:
Accurate information is the key to evaluating the quality and performance of any manufacturer’s LED DISPLAY. However, there are some manufacturers, who produce and sell LED MODULES in a large quantity, and they usually sell to other LED factories/companies.they are using mainly are iron wire bonding led (Mulinseng, HongSeng), for price sake. The competition is getting fiercer, there are small companies who sell inferior quality LED but claim to be a good one. Even now you know those brands and quality level. but you are unable to tell if it is real. After a few months running, the display will bleed you on the maintenance cost. Visionpi provides LED verification services, we can be your professional QC team to help you with the sourcing and inspection and bring lower purchase cost and guaranteed quality.check more our services.